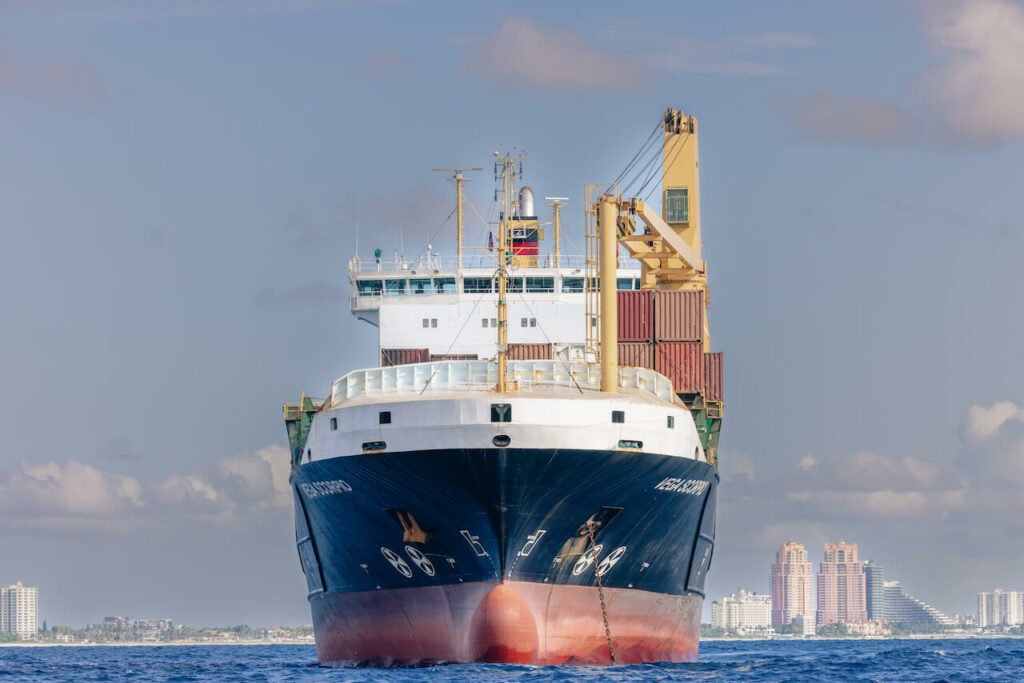
From concept to operation
ALS INSTALLATION
COMPLETE INSTALLATION DESIGN WITH IN-HOUSE RESOURCES
Design process for Shipglide ALS
Shipglide’s engineers and project managers have the ability to take your Shipglide air lubrication system from early concept design to completed installation using in-house resources, without the need for third-party services. The in-house capacity results in an efficient design process with reduced cost and product delivery time for our clients.
THE PROCESS
1. FIRST IN FLEET — INITIAL DATA COLLECTION | The first step in an Shipglide ALS installation is working together with the client to identify which of their vessels would benefit most from an air lubrication system. If historical operational data is available, we’ll start work there; if not, our team can quickly install a flyaway kit at any planned port visit. This performance data provides Shipglide engineers the operational factors for concept design.
2. INITIAL CFD MODELING | Once a vessel is selected, our engineers create a custom CAD model of the vessel for hull geometry. The hull form is analyzed with CFD to determine the existing frictional resistance characteristics. The results are verified with the operational data. Shipglide engineers also use the results of these analyses to target air injection points for initial ALS tests.
3. ALS MODELING AND FLOW CHANNEL TESTING | Using CFD, Shipglide conducts analyses to determine optimal air injection locations and flow rates. Testing is conducted in our purpose-built testing lab to validate these CFD models and improve solution accuracy.
4. AIR SYSTEM DESIGN | The air supply system is designed to minimize parasitic losses and leverage existing ship equipment wherever possible, to minimize cost to the client. The compressor or blower will be selected for each Shipglide ALS installation to ensure that the efficiency of the entire system is optimized within the operational envelope set forth by the client.
5. PROJECT MANAGEMENT | Shipglide employs its experienced project managers to oversee the installation of the Shipglide ALS installation. These engineers are backed by the same engineering team responsible for the system’s design, ensuring it is installed to specifications. Keeping the entire process from concept to installation in-house within the Shipglide team ensures smooth and efficient workflow while maintaining cost control and maximizing system performance.
6. CONTINUED MONITORING AND SUPPORT | After a first-in-fleet ALS installation is complete, vessel performance data is continuously collected to assess the effectiveness of the system in the wide variety of operating conditions a working ship will face. Shipglide engineers will analyze this data and work with the client to identify potential improvements for follow-on Shipglide air lubrication systems installations.
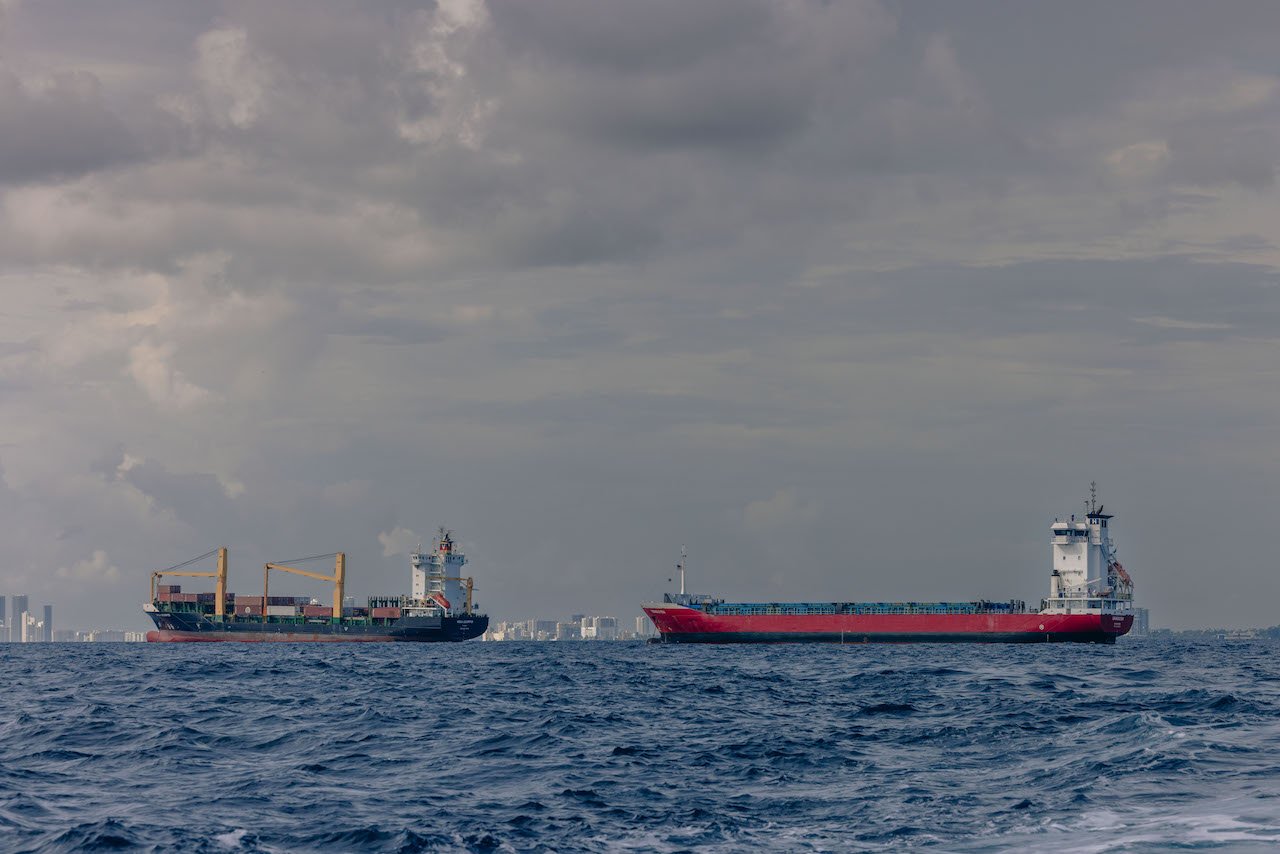
From concept to operation
We study the in-service operation of air lubrication systems and provide verifiable results. Shipglide air lubrication systems can realize real-world, in-service, operational fuel reductions of up to 10%.
THE COMPLETE PICTURE
We supply world-class air lubrication solutions to vessels of all types and sizes
Computational fluid dynamics
Shipglide conducts CFD analysis for every ship type using cutting-edge CFD software and in-house CFD experts
Big data
Shipglide analyzes ship data to confirm fuel savings achieved through its air lubrication systems
Testing lab
Shipglide has the only testing lab dedicated to designing, optimizing and verifying air lubrication system performance
ALS IP and patents
Many of our new cutting-edge concepts have been thoroughly tested, validated, and are now under multiple patents
Installation
Our engineers and project managers have the ability to take a Shipglide ALS from early concept design to completed installation
ALS optimization
We have conducted test cases to demonstrate the potential for analyzing the resistance reduction effects of the Shipglide ALS