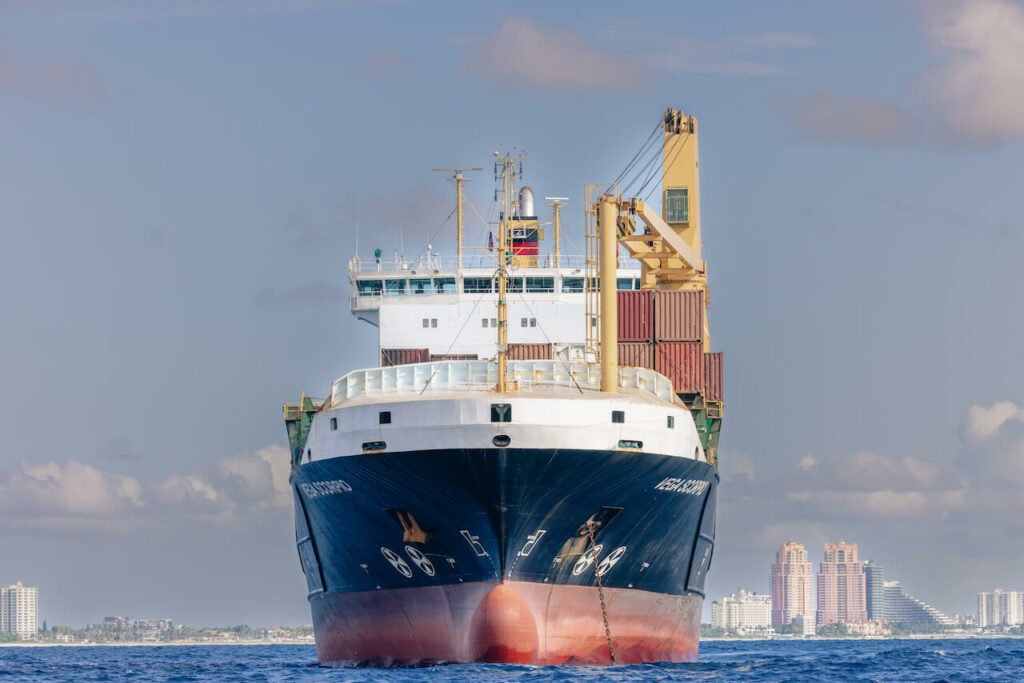
Computational fluid dynamics
OPTIMIZATION
COMPUTATIONAL FLUID DYNAMICS
Full-scale vessel resistance and propulsion power predictions
Computational fluid dynamics (CFD) is a powerful software tool used in a wide variety of applications including aviation, automotive design, turbo machinery, and maritime applications. In the maritime domain, uses include full-scale vessel resistance and propulsion power predictions. The capability of CFD has progressed rapidly and often the results of CFD analyses are more accurate than contemporary model tests in tow tanks.
Shipglide has conducted test cases using CFD to demonstrate the potential for analyzing the resistance reduction effects of Shipglide ALS installations.
A test hull similar to that of a cruise ship was simulated to run at 17 knots in calm water. The vessel was free to heave and pitch, identical to a standard calm water resistance test conducted in a towing tank.
The resistance of the bare hull was determined and the hull was modified to have a slot through which air was injected.
The slot and air injection parameters were then modified to maximize the resistance reduction effect while minimizing the required air injection rate.
SUMMARY OF RESULTS
This simple CFD study shows that more air does not necessarily result in lower resistance. It is more important that the air be distributed to maximize its effectiveness.
In the ALS Version 2 study, the smaller injection slot with a lower air injection rate provided more than twice the resistance reduction effect of the ALS Version 1 study.
BARE HULL
Total Resistance: 945 kN
ALS VERSION 1
Injection Slot Width: 22 m
Air Injection Rate: 6 kg/s
Total Resistance: 896 kN
Resistance Reduction: 5.2%
ALS VERSION 2
Injection Slot Width: 15 m Air
Injection Rate: 5 kg/s
Total Resistance: 819 kN
Resistance Reduction: 13.4%
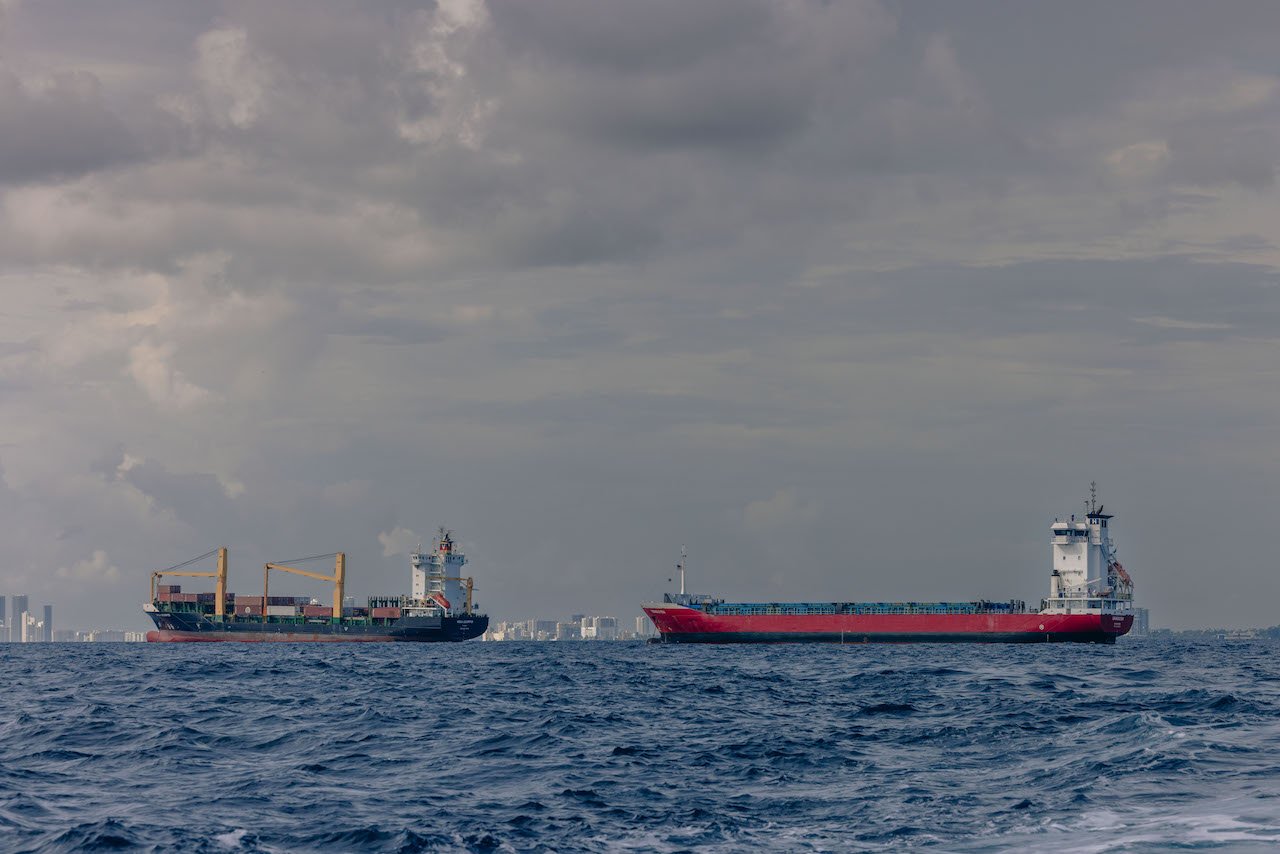
Reduce greenhouse emissions
Through detailed CFD analysis, we optimize the ALS system for your hull form, providing optimum fuel savings and greenhouse gas reductions
SUMMARY OF RESULTS
POWER REDUCTION | Decreasing a vessel’s resistance decreases the amount of power required to drive the vessel. This reduces the vessel’s fuel consumption. Reducing fuel consumption reduces the cost to operate the vessel. Therefore, all other factors held equal, a decrease in vessel resistance results in a direct reduction of cost.
THE COST OF AIR INJECTION | Compressors or blowers are required to force air out of a vessel’s hull. The higher the air pressure and the more air being injected, the more power required to drive the system. This power must be accounted for when designing the system. If the compressor requires more power than the air injection is saving, the system isn’t useful.
OPTIMIZING THE NET POWER REDUCTION | The net power is simply the power saved by the ALS system, minus the power required to achieve that saving. In any given condition, there is an optimal point at which the net power requirement is minimized. In other words, more air would cost more than it would save and less air would provide lower savings than the system is capable of.
SUMMARY OF RESULTS
OPTIMIZATION STUDY | The ALS Version 2 hull was used in an optimization study, again utilizing CFD. The same hull model and injection slot parameters were used, with the vessel running at 17 knots as in the previous simulations.
The air injection rate was varied and a required propulsion power curve was developed from the resulting data. The required compressor power was calculated for each injection rate and a corresponding net power curve was created. The propulsion power curve is depicted in orange, while the net power curve is depicted in blue.
STUDY RESULTS | The gross propulsion power is minimized at an air injection rate of approximately 5 kg/s. However, the net power consumption is minimized at a lower rate of approximately 4 kg/s. This is the optimal operating point for the system at a vessel speed of 17 knots.
This study further highlights the importance of optimizing the air lubrication system to provide the maximum environmental and economic benefit, rather than minimizing the vessel’s resistance. The point of minimum resistance may require more power than it’s worth.
Energy net = EnergyALS - Energy parasitic air supply
INJECTION AIR ENERGY BALANCE
The ultimate contribution of an ALS system to reducing fuel consumption, reducing greenhouse gas emissions, and increasing ship efficiency is the reduction in viscous drag of the ship due to the air bubbles less the energy required to inject air out of the ship bottom to generate the air bubbles.
This is known as the air lubrication system energy balance. The contribution of the air lubricating bubbles to reducing energy consumption attributed to the main ship propulsion is reduced by the increased energy consumption of the auxiliaries which drive the ALS air compressors.
A successful ALS design must realistically consider the parasitic load of generating the source air. Every effort to minimize this parasitic load serves to directly increase the overall impact of the ALS system towards reducing fuel consumption, reducing greenhouse gas emission and increasing ship efficiency.
THE COMPLETE PICTURE
We supply world-class air lubrication solutions to vessels of all types and sizes
Computational fluid dynamics
Shipglide conducts CFD analysis for every ship type using cutting-edge CFD software and in-house CFD experts
Big data
Shipglide analyzes ship data to confirm fuel savings achieved through its air lubrication systems
Testing lab
Shipglide has the only testing lab dedicated to designing, optimizing and verifying air lubrication system performance
ALS IP and patents
Many of our new cutting-edge concepts have been thoroughly tested, validated, and are now under multiple patents
Installation
Our engineers and project managers have the ability to take a Shipglide ALS from early concept design to completed installation
ALS optimization
We have conducted test cases to demonstrate the potential for analyzing the resistance reduction effects of the Shipglide ALS